
Manufacturing ProcessesDesign ConsiderationsTypes of RubberUses & ApplicationsRequest Your Custom Washers
Rubber washers add extra stabilization and weight distribution to parts held together by screws. Fastened screws generate a lot of pressure to hold fixtures in place. This can be dangerous if the pressure remains on just a small area; the fixture is more likely to break or experience stress along that fixture point. If the fixture point has an irregular shaped surface, that can also be dangerous because the screw will use an even smaller area to support the pressure or it will continually vibrate along the uneven contact points.
Rubber washers smooth out the contact surface that the screw bites into for more secure contact and less risk of vibration or malfunctions. It also widens the area for pressure distribution. Since rubber washers have a sealing effect, they also serve to weatherproof projects and help prevent leaks or unwanted water exposure.
Rubber washers offer superior performance compared to metal and plastic varieties. Rubber is pliable and flexible, which facilitates a tighter fit on a wider variety of parts. Screws can also push slightly into the surface to create a tight seal. Rubber is also more cost-effective than metals that offer a comparable degree of resistance to chemical damage, temperature extremes, and weather effects.
How are Rubber Washers Made?
Manufacturers start with raw rubber buns that they cut and shape into rubber gaskets before hardening them into a durable final project. That final hardening process is called vulcanization, and this process uses a combination of heat and pressure to chemically alter the rubber into a fixed, long-lasting shape.
Vulcanized rubber shrinks and may slightly change shape, so manufacturers need to take the changing dimensions into account when creating the initial uncured washer workpieces. Extrusion and die-cutting are the two most common processes for creating raw rubber washers.

Extrusion
Extrusion uses a plate with a distinct cutout that forms the cross-sectional shape of the extruded workpiece. Manufacturers force uncured blocks of rubber against the extrusion tool and the pressure squeezes the rubber out the other side of the tool in the exact shape of the cutout. The rubber will then be cut into specific lengths and/or thicknesses with identical cross-sections.
Rubber can swell during the extrusion process, but experienced manufacturers create extrusion dies that take this reaction into consideration to ensure the part has the right dimensions for processing. Advantages of rubber extrusion include:
- Minimal product waste. The material is pushed through a die, so no excess material is cut away, discarded, or chemically altered.
- Customizability. Rubber extrusion can accommodate almost any shape or specifications within tight tolerances.
- Cost-effectiveness. Rubber washers are a low-cost, flexible alternative to metal washers. Extrusion processes also keep the total cost of production low.
Die-Cutting
This method is similar to stamping. Manufacturers split raw rubber buns to the desired thickness so they have sheets of workable rubber. Next, they feed the raw rubber sheets into a die-cutting machine that punches out the washers based on the dimensions of the washer die.
The advantages of die-cutting rubber washers include:
- Simpler design configurations. Stamping out rubber washers doesn’t make the rubber material swell, so it’s faster and easier to create the die plate.
- Option to add adhesive layers. The first step of the die-cutting process changes the rubber buns into thin sheets, so manufacturers can quickly apply materials along the faces of the washers before cutting them out. One popular option is applying pressure-sensitive adhesives (PSAs) so every washer has a sticky layer without slowing down the manufacturing process.
Both production methods are cost-effective and offer companies a great deal of control over their specifications and end products. Since the washers are machined before vulcanization occurs, any leftover material can be collected and repurposed.
Design Considerations
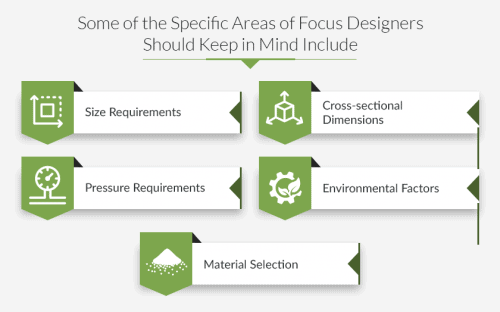
Designing a rubber washer presents several challenges. Each product needs to have the right dimensions to adequately reinforce a fastening point, enough material to create a tight seal, and the right type of rubber to balance product features with production costs. The dies and extrusion molds also need to be precisely designed to account for the impact of vulcanization on the washer’s shape, size, and cross-sectional dimensionality, as well as the extrusion-based swelling effect.
Some of the specific areas of focus designers should keep in mind include:
Size Requirements
The surface area of the washer needs to be big enough to accommodate the screw head and potential nut fasteners, as well as the fastening hole in the fixtures or parts themselves. The hole in the washer also needs to be big enough for the shaft of the screw. Designers should also strive to keep the surface area to a cost-effective minimum so the washers don’t have excess material that drives up the cost of the project.
Thickness also matters. If the washer isn’t thick enough to fix the unevenly matched surfaces between two fastened parts, it won’t work effectively. It also won’t be able to prevent leaks or rattling from vibration.
Cross-Sectional Dimensions
The end-to-end dimensions of a washer change when the washer is compressed. Designers need to create designs with the right dimensions when the part is at rest and when the part is in use.
Pressure Requirements
Manufacturers can use a variety of rubber types to create seals for different applications. The material needs to be soft and pliable enough that it can fit against uneven surfaces and close any gaps, but not so flexible or soft that water can push its way around the seal. Every design requires a rubber material that provides just the right amount of resistance to pressure.
Environmental Considerations
Pressure isn’t the only unique factor that can impact the washer’s long-term effectiveness. Environmental factors such as temperature and weather must be part of the design considerations, as well. The washer may need different materials and finishes depending on whether the end application is indoor or outdoor. If the washer is also being used as a seal to contain water or more volatile chemicals, designers will need to carefully select a material that won’t degrade due over long-term contact with the particular chemical.
Material Selection
Every rubber substrate is slightly different. They offer different features and advantages that can be tailored to specific applications, including:
- Abrasion resistance
- Cushioning
- Impact resistance
- Open structures for selective permeability
Selecting the Right Type of Rubber
Some of the most popular rubber material options include chloroprene, EPDM, natural rubber, neoprene, nitrile, PVC, SBR, and silicone.
Solid Rubber
At Thomas A. Caserta, Inc., we specialize in creating durable, solid rubber washers. Other forms of rubber include sponge rubber and foam rubber, but these forms of rubber have air pockets or breathable cellular structures. Foam rubber is blown during production and has open cells that make the material a poor choice for water absorption. These rubber types are too pliable and don’t create a strong seal.
Conversely, solid rubber has a more compact cellular structure and can better distribute force and pressure. Solid rubber can also resist abrasion, indentations, and stress. Given that solid rubber can be produced to varying degrees of hardness, solid rubber washers can be soft, hard, or anything in between.
Applications
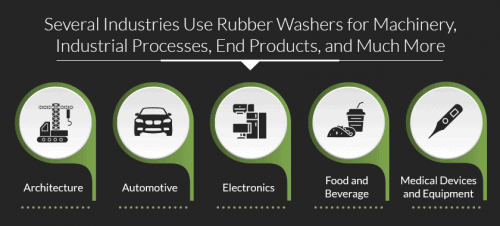
Almost every industry has countless applications for rubber washers. The following industries use rubber washers for machinery, industrial processes, end products, and more:
- Architecture. Architectural washers can help maintain building envelopes by preventing leaks and airflow around exterior openings like vents, windows, and utility openings.
- Automotive. Rubber washers can seal gaps to prevent dirt and water from clogging sensitive parts, as well as prevent fluid leakage.
- Electronics. Electronic assemblies need rubber washers that can prevent contamination, especially in outdoor environments. In some applications, rubber gaskets can also reduce electromagnetic interference.
- Food and beverage. Rubber washers that meet FDA and USDA production standards are used in everything from ovens and cooling systems to peristaltic pumps.
- Medical devices and equipment. Most medical applications require specifically designed rubber washers that meet strict manufacturing standards. This includes production in a Class 10,000 cleanroom.
Contact the Rubber Washer Experts at Thomas A. Caserta, Inc.

Thomas A. Caserta, Inc. specializes in fabricating solid rubber washers. Our team handles end-to-end production using extrusion or die-cutting. Our washers have excellent dimensionality, long-lasting endurance, and customizable features for special projects. Request a quote above to learn more or to start your order.