Thomas A. Caserta, Inc. is a leading manufacturer of rubber products used in multiple industries for different applications by fabricating and cutting rubber to your needs. Our in-house facility is fully equipped with state-of-the-art equipment to create high-quality products to achieve your desired results.
We also offer a fully customized solution for clients who have specifications and requirements to meet. We are dedicated to providing the best customer service, ensuring our clients’ satisfaction always comes first.
Our team of engineers ensures to follow stringent quality controls during the manufacturing process while meeting deadlines. We understand how essential it is to deliver on time, especially in demanding operations. Fortunately, we can give that to you to enhance customer satisfaction.
Premier Rubber Manufacture Services at Thomas A. Caserta, Inc.
Some of our most popular products include washers, gaskets, tubing, cords, and bushings. Each can be achieved with the right manufacturing capability. These include guillotine cutting, die cutting, water jet cutting, and extrusions.
At Thomas A. Caserta, Inc., these highly specialized services are designed to create industry-standard rubber products for a wide range of sectors to support their varying projects and operations. With our expertise, knowledge in rubber products, and the various backgrounds of each industry, we know what type of outputs are best for the numerous applications.
Our services include the following:
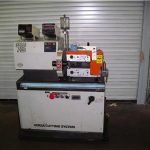
One of the most cost-effective methods of cutting rubber is our high-speed, on-demand rubber-cutting services. It’s also an ideal manufacturing technique for producing rubber washers and gaskets. The machine is equipped with flying knife types of cutters, which cut tubing into gaskets and washers at incredible speed with minimum waste.
Apart from rubber washers and gaskets, our on-demand rubber-cutting service is also ideal for spacers, bushings, discs, and stand-offs. Since it employs a simple cutting tool, it can handle most standard and specialty materials.
Benefits of our high-speed, on-demand cutting services:
- Minimal waste
- Cheaper than other alternatives
- Fast and ideal for large production runs
- Efficient cutting process
- Precise tolerance
- Also great for prototyping purposes
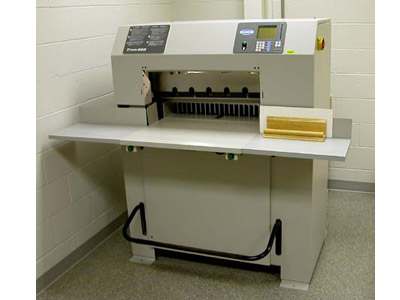
For most rubber washers, high-speed guillotine cutting rubber products is the best option. We have machines capable of multiple tube cutting simultaneously and can be adjusted to cut different shapes, sizes, and thicknesses.
Our custom-made guillotine rubber-cutting equipment is designed to adhere to our unique system and process. Through this, we can produce up to 9,000 washers per minute. It’s ideal for industries looking for consistent washers in large quantities while delivering in a quick turnaround time.
Benefits of our high-speed guillotine cutting services:
- Equipped with steel blades for right-angled cuts
- Economical production speeds vary
- Faster turnarounds
- High production volume of washers with consistent results
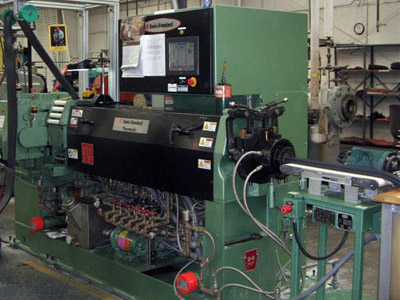
We have rubber extrusion services ideal for customized solutions, such as custom rubber tubing and cords. This process involves softening and pressurizing the rubber materials until it becomes pliable. After that, it’s forced into a die, which results in a continuous material with the same consistent cross-section.
Our rubber extruders are unique and are equipped with the latest screw and barrel designs. It also employs the best control systems, allowing us better to facilitate the production process in our in-house facility.
Benefits of our customized rubber extrusion solutions:
- Resistance to heat, abnormal wear and tear, and friction
- Withstands normal abuse
- Cost-effective due to low waste
- A versatile solution for various materials
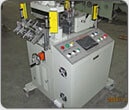
Our die cut services refer to cutting material into different shapes and forms by pressing a metal die on the rubber material. It has the same principle as a cookie cutter, where the rubber material is the dough, which is cut into smaller pieces. Die cutting is an efficient and quick process that can quickly recoup the initial costs due to its excellent quality, efficiency, and speed.
Benefits of die cutting:
- Highly customizable
- Affordable in bulk orders
- Can achieve complex shapes
On the other hand, waterjet cutting utilizes a highly pressurized jet of water to cut the rubber material through a supersonic waterjet stream. As the water leaves the nozzle, the speed increases three times compared to the speed of sound.
Benefits of water jet cutting:
- Extreme precision and accuracy
- Environmentally safe than other techniques
- Cost savings due to ease of setup and fast transition times
Die cutting and water jet cutting are both ideal manufacturing techniques for rubbers, and we have the resources to deliver both services easily. Our team of experts is highly knowledgeable, ensuring you get the best method for your particular applications.

Our lathe cut rubber services involve the use of the lathe, which is the machine used to rotate a workpiece to perform the cutting process. Here, a mandrel is used and inserted in an extruded rubber, and then the material is cut into the desired dimension while the mandrel is rotating in the lathe.
In addition to the lathe, we also have the latest grinders to finish the material’s outer surface while following precise tolerances.
Benefits of using a lathe machine:
- Accurate and precise outcomes
- Less lead time
- Unrivaled range than other rubber manufacturing methods
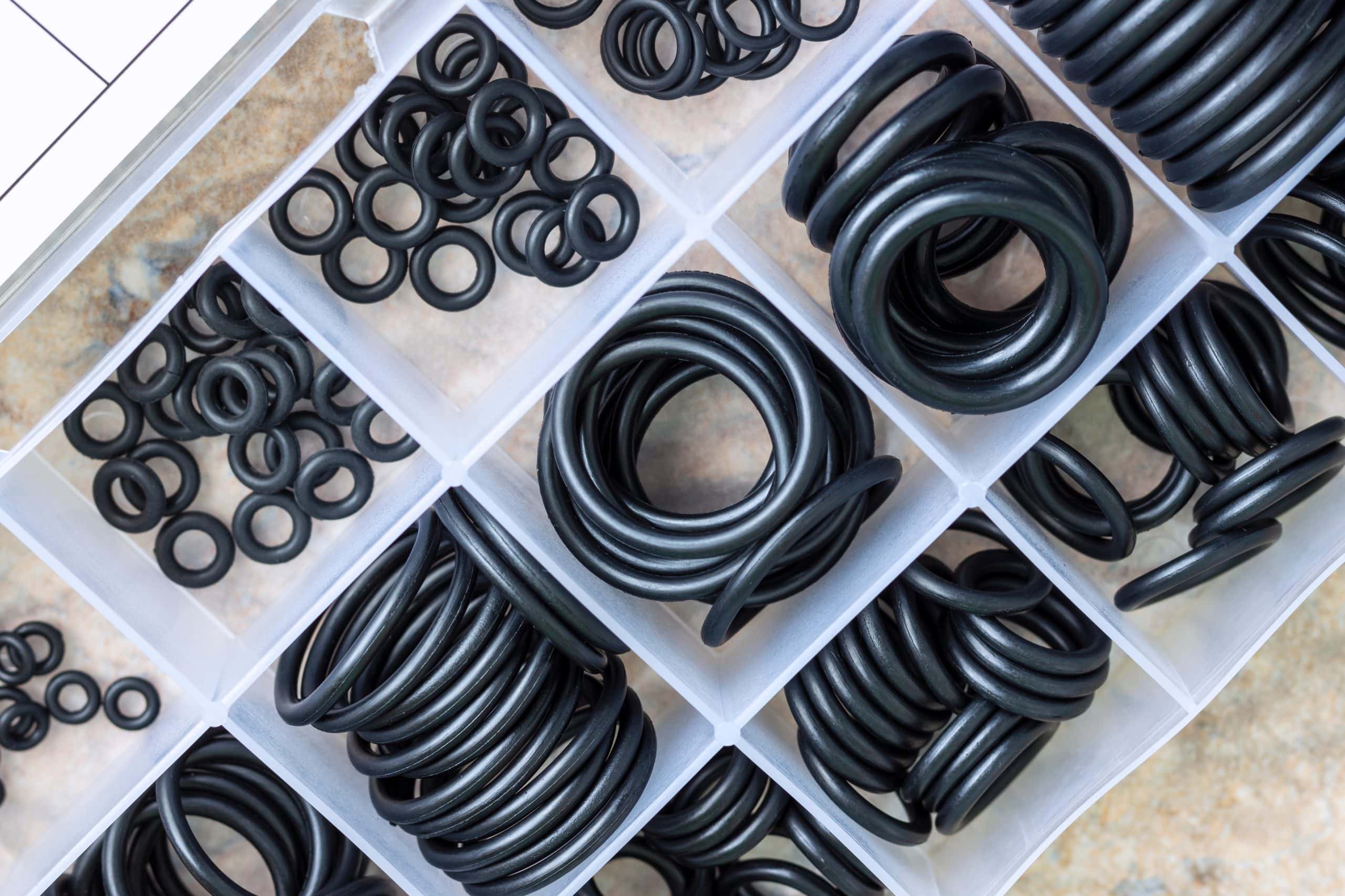
We utilize silicon materials to create high-temperature gaskets and seals while employing our different cutting rubber services. Silicon is a durable elastomer that offers incredible heat resistance, resilience, and electrical insulation against other types of rubbers. These features made it the perfect option for industrial-grade gaskets and seals used in various harsh operations by demanding industries.
Silicon-made rubber gaskets are ideal for machines and equipment that deal with high temperatures. These are also seen in operations that involve combustibility. However, we also have other materials suitable for high-temperature applications.
Material our rubber gaskets are made of for high temperatures:
- Conductive silicone
- EPDM
- Silicone coated fiberglass
- Silicone
- Fluorocarbon
- Fluorosilicone
These materials can work with varying high temperatures. Determining the suitable material and cutting rubber capability for your sector highly depends on your facility’s needs. Fortunately, our team of experts can assist you in selecting the most suitable option for your operations.
Why Choose Thomas A. Caserta, Inc.?
We’re a leading manufacturer of rubber products through our reliable services and capabilities. Whether you need simple tubing or high-temperature seals, we can easily create them through die cutting, waterjet cutting, high-speed guillotine and on-demand cutting, and lathe rubber cutting.
In addition, we use numerous rubber materials, which will meet the needs of various industries. Some of these sectors include aerospace, automotive, plumbing, OEM, electrical, and more. If you have any rubber product needs, always choose Thomas A. Caserta, Inc. for the best rubber product outcomes!
Trust Us to Manufacture Your Desired Rubber Products
Searching for a rubber product that can adhere to your various systems and operations can be daunting, especially if you have special processes that can affect your product output. Fortunately, Thomas A. Caserta, Inc. offers different cutting rubber services to ensure you receive quality and industrial standard rubber products to help your operations run smoothly without downtime.
If you have any questions or concerns about our services and products, don’t hesitate to contact us today. Our team of engineers and operators is equipped to provide expert advice while following your strict demands for your facility to ensure complete satisfaction. You may also request a quote, and we can send estimates for your following projects.